What are the different Lean Six Sigma Tools?
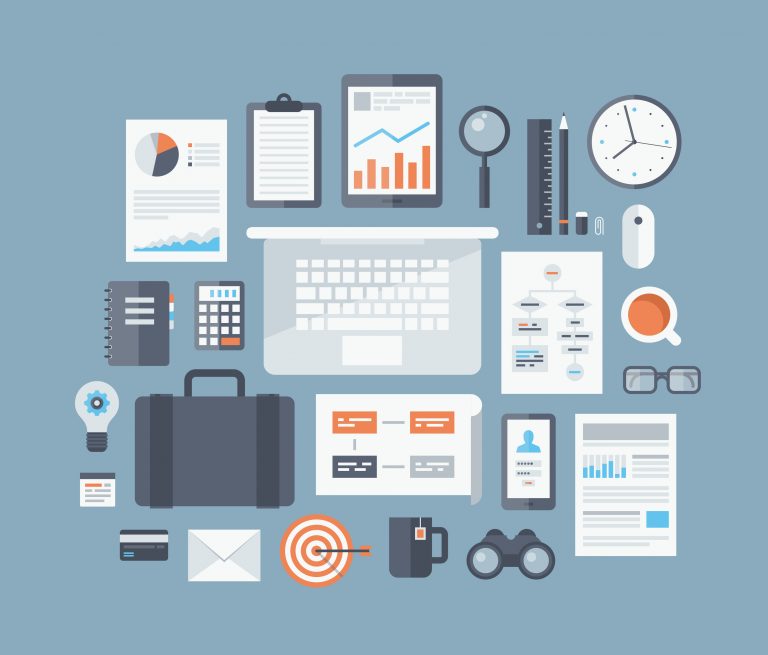
Tools play a very important role in Lean Six Sigma, as their use help in obtaining cost, speed as well as leaps in quality. Very much like Six Sigma, the DMAIC model is used to make improvements.
Today we will look into the tools used in Lean Six Sigma:
- SIPOC: The full form of this term is Suppliers, Inputs, Process, Output, and Customers. Basically, SIPOC is a diagram that provides visual answers to the questions that are needed to understand the process. The resulting diagram is as important as the steps involved in creating this diagram and the involvement of team members in ides generating and brainstorming sessions.
- Stakeholder Analysis: Using this tool various stakeholders are listed and the impact of the improvement project on each assessed.
- Voice of the Customer (VOC): VOC tools such as interviews, focus groups, suggestion boxes are used to provide data on representing customer requirements and viewpoints. Kano analysis is used to convert this raw data into qualitative and quantitative data.
- The Cause-Effect Matrix: The tool is used to tabulate against effects and calculates scores which are eventually used to rank the causes. This tool is used to measure the matrix that is used to select which inputs to focus on.
- Data Collection Plan: This tool includes all the decisions related to what data to collect, the determination of sample size, the identification of data sources as well as the development of data collection sheets and the assignment of data collection duties among members of the team.
- Pareto Chart: This tool is a bar chart where the horizontal axis represents categories. A Pareto chart is a tool that focuses on the team’s effort on the problems that are most important.
- Scatter Plots: In this tool, two variables are plotted against each other on a graph, which provides a visual indication of how well the variables correspond to each other.
- Fishbone Diagram: Using fishbone diagram tool a large arrow is drawn along with the effect of whose causes are being analyzed displayed on the right at the end of the arrow. When this information is available, detailed causes are brainstormed and indicated for each category against the corresponding branch.
- Regression Analysis: This tool can also be regarded as the mathematical equivalent of the scatter plot. In regression analysis, an equation is derived in order to express the dependence of one of the variables on one or more others.
- Mistake Proofing: When the proper design of the processes and equipment are used, the possibility of errors is totally eliminated. Examples of mistake-proofing are designing online forms that cannot be submitted in case of incomplete or incorrect data.
- Testing of Hypothesis: This tool is used for testing the validity of assumptions, which might be related to the impact of causes on effects.
- Project Management: Whenever a solution is agreed upon, it is implemented in the form of a project. This solution will then require the use of project management tools such as communication, planning, monitoring, and risk assessment.
- Standard Operating Procedures: New operating practices, which are improved, will now be codified in an operating manual that operators can refer to. This manual prevents slippage that might again lead to inefficient practices.
- Statistical Process Control: This tool is used to prepare control charts that reflect the improved capabilities of the process. This control chart is used to monitor performance overtime.
- Visual Management: The basic principle of visual management is that an employee should be able to walk through the work area and then come away with 90% of the information. 5S organization, illustrations of process steps that are placed close to the process as well as SIPOC diagram and value stream maps are used to achieve visual management.
References:
http://ezinearticles.com/?Some-Lean-Six-Sigma-Tools—Define-and-Measure&id=153995
http://ezinearticles.com/?Some-Lean-Six-Sigma-Tools—Analyse,-Improve-and-Control&id=162081