Six Sigma and DMAIC in Focus: I – Improve Your Six Sigma Project
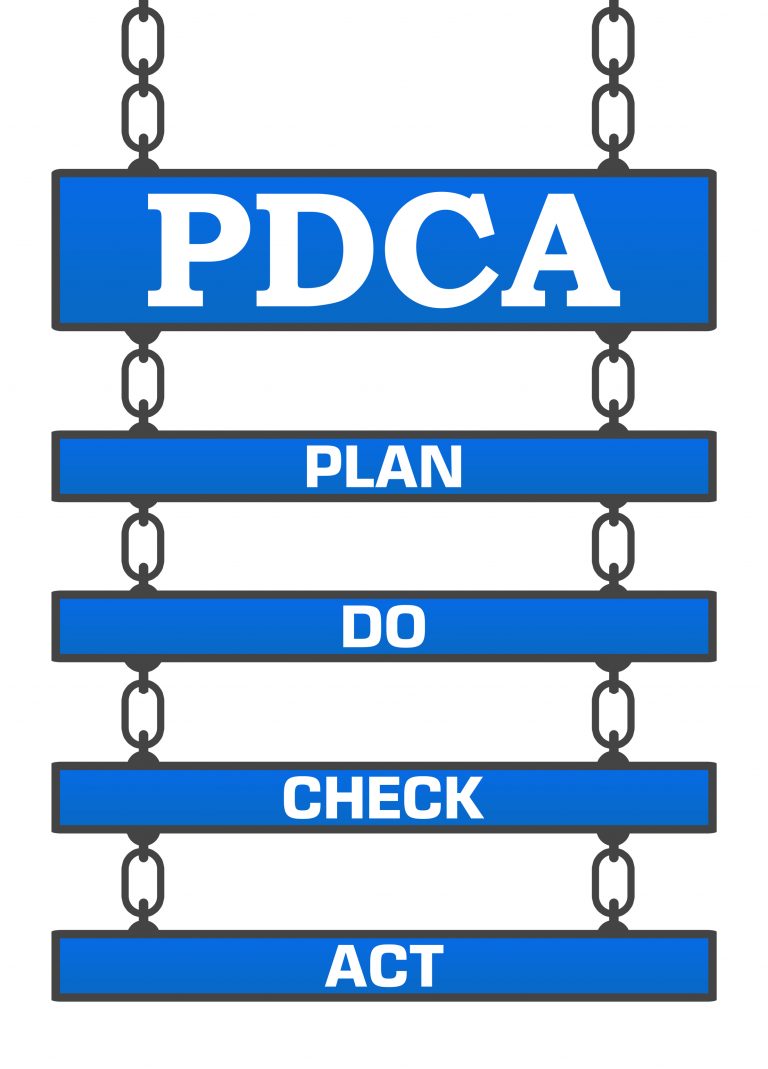
This article is the fourth part in our series on the principles of Six Sigma, focusing on Improve within the DMAIC framework. You can find the rest of our series here.
Day four now sees us approaching the end of our DMAIC in focus series. Today, we will be looking at how to improve ourselves, and our projects, with Improve.
Improve Equals Efficiency
Improve builds on the stages before to deliver results. It’s what all of your hard work in defining your problems, measuring and analyzing them, has to lead up to. Improvement cannot be implemented without that solid grounding the DMAIC process is known for.
You will spend this phase of DMAIC redesigning the overall process to increase efficiency. If the Improve stage is to run sufficiently, then your process must test its updated design and settings. This, therefore, ensures adequate sigma level is confirmed in the short-term. The “vital few” causes that must be identified in the preceding Analyze stage will also have their operating tolerances established at this point. What tools can you use at this stage of the cycle? Regression, Hypothesis testing, designed experiments, analysis of variation (ANOVA), and simulation. There are probably others, although we suggest starting here.
Problem Solving
Throughout the course of your project, you will encounter a variety of problems. From production, customer service, through to efficiency, and productivity. You can remedy those through DMAIC. To accomplish this, your solutions will need first to be identified and tested, before being implemented into the business’s production process infrastructure.
Also, you will need to be creative here. Creativity is a powerful asset for a Six Sigma project. You will find team-based techniques such as brainstorming, as well as free association, can help you create effective solutions. Try to follow these steps to really drive improvement:
- Create,
- Select simplest solutions,
- Test using PDCA cycle,
- Anticipate avoidable risks based on results using FMEA,
- Create an implementation plan,
- Implement the solution(s).
PDCA Cycle
A fantastic tool for assessing the quality of your improvements is the PDCA cycle. It is a four step process, which provides empirical data to support your approach. What does it stand for, and how do you use it? We’ve put together a short overview for you:
- Plan. You should always plan how your improvement will function. Take a look at the process you want to improve, and plan a limited rollout.
- Do. To know is not enough, you must apply. Arguably the master of modern Kung Fu, Bruce Lee, gave us this particular nugget. Kaizen philosophy and martial arts aside, it’s a great mantra for the modern Six Sigma practitioner. Act on your plan. Apply yourself.
- Check. Once you have data from Do, you can start to check the effectiveness of your solution. Does it address the root cause, or does it only tackle a superficial cause?
- Act. Once you have a plan, have tested whether it is fit-for-purpose, and have checked this, you can act.
You should also know what separates long- and short-term sigma levels when entering the Improve stage of DMAIC. Time to get your calculators out, as estimating long-term value in Six Sigma is done by deducting 1.5 from the short-term value. This is necessary since the 1.5 sigma mean shift (the accepted method of assuring the product is defect-free) takes place over a long period of time. Therefore, your short-term processes will have long-term values of 4.5, their estimated long-term defect rate sitting at 3.4PPM.
In Conclusion
The aim of Improve is to demonstrate six standard deviations between the process mean and closest specification limit. The specification limit acts as the baseline at which your product or service does not satisfy the expectations of your customer. This is often a feature of the product that can be measured, like the amount of heat lost through a glass window.
Finally, remember, the overall outcome of your Six Sigma project is to deliver measurable improvement. Most of all, you must use every ounce of your creativity to achieve this, through thorough application of Six Sigma values.
Contact us at 6Sigma.us and find out how we can positively change the culture and operations of your manufacturing unit. We offer Green Belt and Black Belt training programs, as well as a Master Black Belt program.