Beginner’s Guide to Value Stream Mapping (VSM)
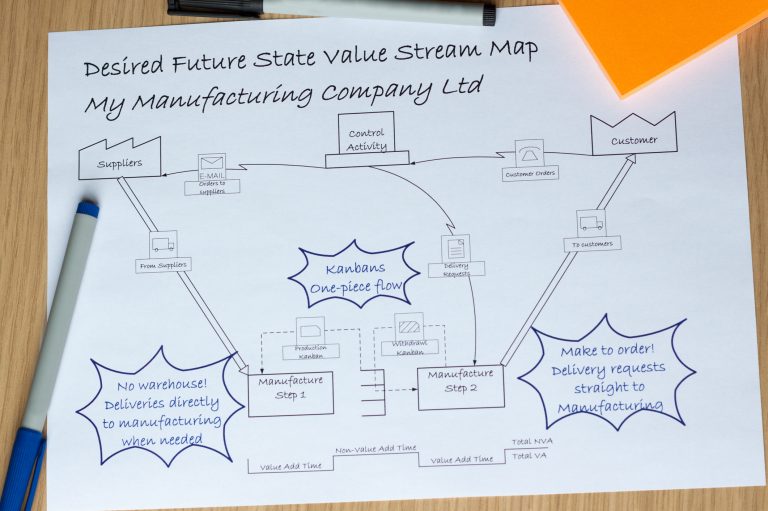
We look now at the Lean method of Value Stream Mapping (VSM). This is a method where you analyze a current state and design a future state where you look at events from the very beginning of the process to the very end with delivery to the customer. This can involve a product or service. Toyota uses this method and calls it Material and Information Flow Mapping.
We should note that Value Stream Mapping can apply to many environments and processes that include manufacturing, healthcare, software development, supply chain operations, logistics, office processes, and product development.
Some techniques
When you create Value Stream Maps you typically use a standard set of symbols. No one set is of symbols is required. The team can use whatever symbols help them. This can be as simple as squares and arrows.
Here are some techniques that can help:
1. Put value added steps in the center of the map – to represent the value stream
2. Include non-value added material outside of the center part – to represent the waste stream
Remember that the Value Stream Map can represent a flow of materials and a flow of information. You can see (from such a map for a process) where you have issues such as delays and excess inventory.
More techniques
Here are some general best practices you can use as you develop Value Stream Maps:
• Make this a team exercise.
• Include those who do the work.
• Make the leader someone with experience in creating this map.
• Create the map with the entire team present.
Here are some typical steps in creating the map:
1. Decide what to map and look at products that use the same process.
2. Decide which products to look at. For example, if your company makes plastic cups, you could pick the product with the current highest volume or the product projected to have the highest future sales.
3. Limit what you will map. Decide if you will map the entire supply chain or just part of it.
4. Decide on your approach. You could start with the customer and work to the starting point. Or you could start with raw materials and end with the customer.
5. Add information flow. This can include how a customer orders products and how the organization makes sure the customer gets what they ordered.
6. Collect data. This can include data about inventory, number of people involved in production, scrap rates, and how long it takes to create a batch.
7. Add data to your Value Stream Map.
Once you have a map developed you can interpret the map to see where you have problem areas that can include:
• Too much inventory
• Scrap
• Poor quality
• Long setup times
Addressing the problems
Once you create the map and start analyzing, you should have an idea of your final goal. This goal could be an improved process with less scrap. To reach this ideal your team can work together to address issues one at a time or several issues at a time. Here are some approaches to consider.
1. Plan improvements with each taking a month or two
2. Use your Value Stream Map to explain what you will do
For example, an improvement could be to cut setup time from 6 hours to 5 hours. You could indicate this on the Value Stream Map.
You can use a simple spreadsheet to assist with Value Stream Mapping. For example, you could create a worksheet showing actual steps in a process. Indicate what the work is, who does the work, and how much time the work takes. These worksheets can help you analyze your process and how you can improve it.
Let’s review
We looked now at the topic of Value Stream Mapping and some practices that can help with developing these maps and the improvements they can facilitate. To see some examples you could go to http://leanmanufacturingtools.org/551/creating-a-value-stream-map/ and http://courses.washington.edu/ie337/Value_Stream_Mapping.pdf
You can go to https://www.6Sigma.us/six-sigma-training.php to learn more about our training solutions.