Important Steps of Lean Manufacturing Processes
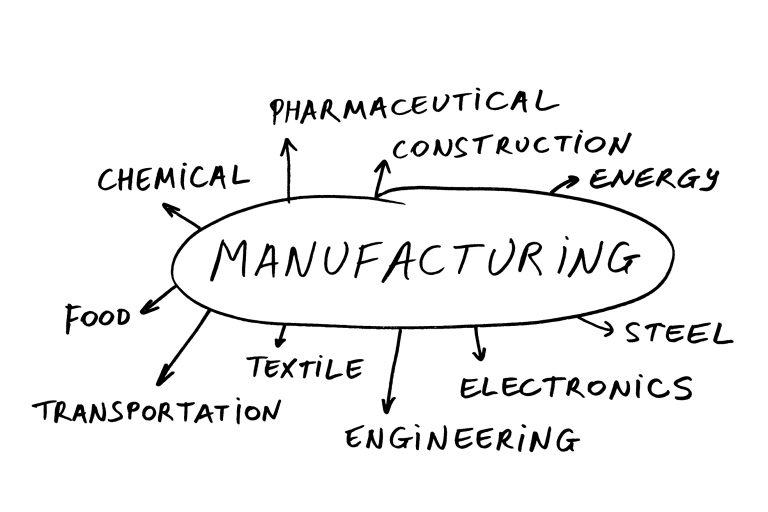
Lean manufacturing processes help businesses eliminate waste within their own manufacturing systems. This waste (also known as muda) is typically a byproduct of variation and instability within production, i.e. the quality of components used to make a car will vary in their abnormality, depending on your supplier. The higher DPM (defect per million) for the components you use could add up to a fully defective car after a certain amount of time. This can mean huge losses for companies whose customers depend on and expect high quality service. Lean manufacturing helps prevent this. It can be hugely beneficial to maintaining and improving a company’s overall quality, as, from a client’s point of view, a process or product when is valued when they are happy to pay for it. By using Lean manufacturing, you can ensure your clients and customers have total faith in your ability and service, which will in turn improve sales, company image, and profitability.
Stability is the foundation of the Lean manufacturing process, the overall quality level for a product or service. It can sometimes be compromised, however, which leads to abnormality in production. Six Sigma similarly focuses on eliminating this variation or abnormality (Mura, which means literally, unevenness),and Lean manufacturing also aims to eliminate the waste that both contributes to and is a byproduct of it. Continual improvement is a key feature of the model, with production leveling and standard working carried out simultaneously, wherein the standard process is refined continuously to avoid setbacks in the future. The objective of this is to reduce unevenness that can lead to waste. This is also known as Heijunka, and big companies like Toyota, incorporate these principles into their own manufacturing processes to increase efficiency.
It’s beneficial to incorporate a pull system at this stage in Lean manufacturing, as this focuses your efforts on the value stream generated by the customer, rather than forecasts that may or may not be accurate. Specifying value first will give you an idea of customer perspectives, so you can express that value for items at particular prices, at a specific time. The value stream can be identified using a map for Current State and Future State, and should flow properly to eliminate functional barriers in the production process. The pull system is highly useful here as it allows you to work to customer needs, minimizing the need for a sales forecast. Takt Time is also important here, as it measures the available time in the day divided by the daily units of sales. It is a way of expressing in seconds the potential for improvement, no matter how small. By implementing Takt Time and maintaining other essential elements of the pull system, such as Heijunka, and Kanban, your company can achieve consistent results in continuous improvement. Kanban can only work in continuous production, and relies on the streamlined, stable production processes laid out by Heijunka, in which defects can be seen to instantaneously according to clear criteria. It is also imperative to preventing machine breakdowns, as rapid preventative maintenance and repair will ensure production continues to run smoothly.
All of this will help to achieve One Piece Flow, a fundamental prerequisite for achieving Leanness. Using only one processing unit at a time can bring with it major drawbacks for any organization. Batch manufacturing dictates, regardless of quantities ordered, and for when, multiple batch creation for products, i.e. mobile phones, games consoles, etc., forecasted as being highly profitable. This will enable you to get ahead of demand, Lean principles providing limitless means to reduce waste effort, time, space, and costs. You will soon see the benefit as your company moves quickly towards greater efficiency, for increased sales, and Leaner production.
Stop by and contact us at 6Sigma.us and find out how we can positively help you plan and change the culture and operations of your organization. We offer Green Belt and Black Belt training programs, as well as a Master Black Belt program.