Root Cause Analysis (RCA)– Important Steps
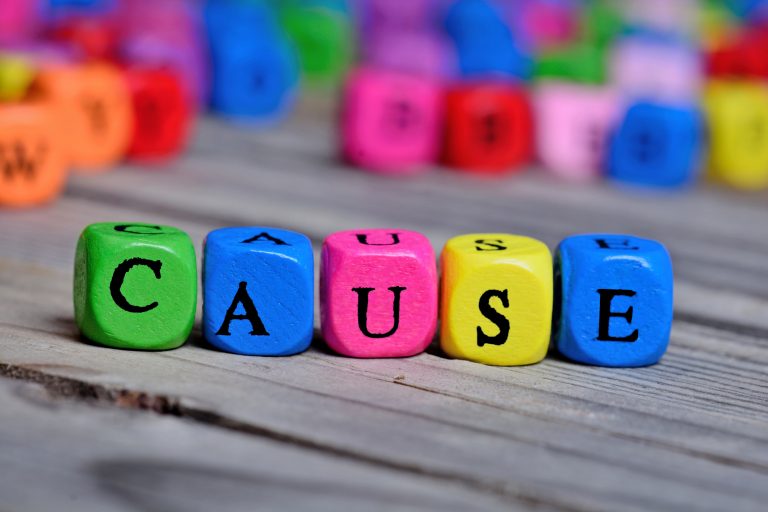
Let’s look now at an important tool used in continuous improvement efforts. The tool is Root Cause Analysis (RCA). We will cover steps you can take when using this tool to help solve problems and resolve issues.
We should note that Root Cause Analysis is a way of finding a fundamental cause for a problem, not just a ways to address a symptom. For example, imagine you are manufacturing plastic cups and scrap 100 of them in a day. A cause of this could be that the technician did not maintain equipment properly. The root cause could be that the maintenance procedure is not clear and the training did not cover maintenance. To fix the problem properly you must maintain the equipment and improve the overall process of documentation and training.
Learn More About Root Cause Analysis Training
We should also note that Root Cause Analysis, when done properly, is an iterative process to help with continuous improvement in an organization. Root Cause Analysis can use approaches that depend on the application. These can be quality industrial applications, safety concerns, process concerns, business processes, and systems approaches.
General principles
Here are some of the general best practices for Root Cause Analysis:
• Make the aim of Root Cause Analysis to determine how to fix a particular problem and other related problems.
• Use Root Cause Analysis in a systematic way.
• Remember a problem can have more than one root cause.
• Keep cost in mind when determining a fix to a problem.
• Keep in mind a fix needs to be sustained.
• Understand that Root Cause Analysis can cause a change to a culture and resistance from those who will implement the change.
Here are some steps to taking action based on Root Cause Analysis:
1. Define the problem.
2. Collect data.
3. Ask why. This means determining the factors that led to the problem.
4. Determine which factors are root causes and not just symptoms.
5. Identify corrective actions.
6. Identify solutions that will help the problem from recurring and do not cause other problems.
7. Implement the solution.
8. Determine if you can use this solution with other problems.
More guidelines
Remember that Root Cause Analysis is one of the basic tools you should use for continual improvement. Your goal using it is to understand an issue and what is causing it. You can then resolve the issue, not repeat the problem, and improve a process.
Here are some guidelines:
• Use Root Cause Analysis as soon as you recognize a problem.
• Do not wait until a problem becomes severe.
• Use Root Cause Analysis in an iterative way.
• Give priority to the problem that is most urgent.
• Be precise.
• Pick a problem that is solvable.
• Use the 5 Whys technique.
When you implement a corrective action to communicate to all involved the:
• reason for the action.
• benefits of the action.
• time needed to implement.
After implementing a solution remember to iterate.
Here are some related best practices:
• Ask if the solution is effective.
• Review the results of the action.
• Modify the action as needed.
• Recognize you may need a different approach if the problem continues.
• Update procedures.
After you update procedures check that everyone is following the procedures. In time revisit the issue to make sure the fix is still working and everyone is following the procedures properly. Remember that training could be involved once you determine a resolution of a root cause problem.
Remember also that when you do a root cause analysis the next step is critical. You must have an effective corrective action plan and a preventive action plan too. Make sure your organization follows the plan, provides proper documentation, trains all involved, and continuously follows up on additional improvements to the process.
We can positively help you plan and change the culture and operations of your organization. We offer Six Sigma Green Belt and Six Sigma Black Belt training programs, as well as a Six Sigma Master Black Belt program.