Lean Six Sigma in the US Army – Toward Efficiency
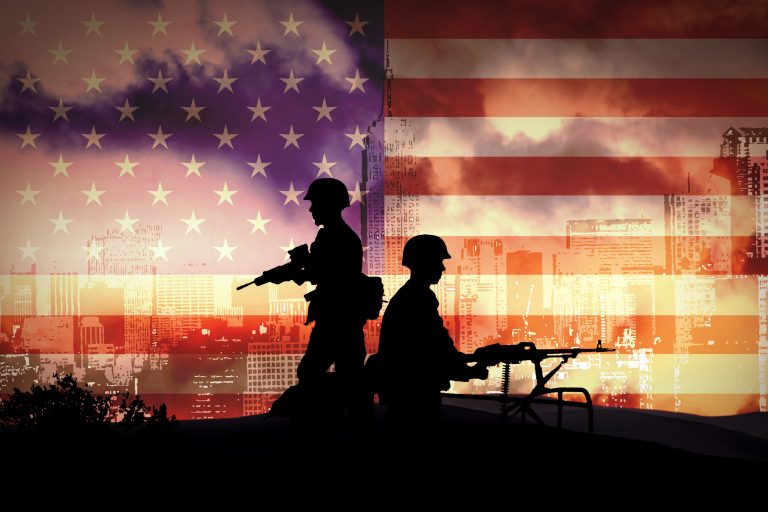
Lean manufacturing combined with Six Sigma have been combined to form Lean Six Sigma. Both are basically techniques to improve business. The concept of Lean manufacturing comes from Toyota Production System while Six Sigma owes its origins to Motorola. Both concepts when combined, can transform organizations.
Elimination of waste and reduction in the time cycles are the goals of Lean while Six Sigma focuses on improving quality and reducing variability. The goal of any business is to maximize shareholder value. This can be achieved by reduction in cost, increase in quality, increase in process speed, a better return on invested capital and improved customer satisfaction. When Lean Six Sigma is applied to businesses, there are significant benefits in terms of improved lead time, reduction in costs and enhancement of quality.
The US Army has adapted the Lean Six Sigma to its growing needs to eliminate waste in time, money and material. To this end, the US Army Installation Management Command or IMCOM for short has drawn up a training program for enhancing productivity and reducing costs.
IMCOM has a training program for bringing about transformation in the US Army through Lean Six Sigma. The curriculum includes awareness and conceptual training on how the concept of Lean Six Sigma fits into the overall strategy of the US Army to make it efficient and productive. Hands-on understanding of the process is given; participants are imparted knowledge on how to identify projects and select them for the purpose of applying Lean Six Sigma. The roles and responsibilities of a Leader are highlighted. The curriculum also includes training in tools and skills necessary for effective and efficient implementation of Lean Six Sigma.
Personnel have divided into Green Belts and Black Belts. Green Belts are taught to be effective team members. They are taught the DMAIC concept of Six Sigma. DMAIC is the acronym for, Measure, Analyze, Improve and Control. Black Belts are those who will use the processes and tools required to implement DMAIC methodology. Black Belts are taught through simulation, case studies, exercises and examples.
The application of Lean Six Sigma in the US Army has resulted in reduction of expenditure and improvement in productivity through contracting, manufacturing, administrative services and recruiting.
The Red river Army Depot at Texas in one such example. The US Army was able to save $30 million on the production of Humvees. The unit upped its production from 3 Humvees a week in 2004 to a whopping 32 mission ready Humvees in a day by 2006.
The Regional Readiness Command at Utah has been able to reduce the cycle time from 90 to 21 days in awards processing. Previously, the deployment preparation time for a battle-rostered unit was 30 days. On account of Lead Six Sigma this time period has been brought down to just 3 days!
LEADS, the system through which army starts the recruitment process of prospectives, has improved on account of Lead Six Sigma. The steps have been reduced from 32 to 11. This has brought down the time taken for the recruitment by 40%.
The repair cycle time at the Pine Bluff Arsenal at Arkansan reduced by 90%. The production of M-40 protective masks increased by 40%, on account of Lean Six Sigma.
There was an $11.9 million reduction of cost in Patriot air defense missile system recapitalization.
At the Corpus Christi Army Depot in Texas, the time taken to rebuild the UH-60 Blackhawk decreased from 256 days to around 70.
In the backdrop of fiscal constraints that the US Army is facing, these cost savings have come in as a morale booster. While, undoubtedly there have been a number of examples of costs savings and improvement in productivity on account of implementation of Lean Six Sigma, more profound has been the impact of the common US soldier. Despite the initial resistance, wherever it has been implemented in the US army, it has met with success.
Wait no more, register today for your Six Sigma requirement. We look forward to seeing you in our upcoming session near you! Find a training option that is right for you by clicking here.