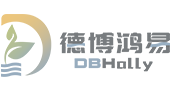
Monthly Management Tips
- Learn from experts every month for free
- Valuable information direct to your email
- Easy to read and you can cancel anytime
There are a lot of terms that are specific to Lean and Six Sigma. If you are unsure about the meaning of a term, please feel free to check our Lean and Six Sigma Glossary for a definition. If you do not find the term you are looking for, please contact us. We would be happy to answer your questions, and we may add your term to the glossary in the future.
Continuous data | Any variable measured on a continuum or scale that can be infinitely divided; primary types include time, dollars, size, weight, temperature, and speed; also referred to as “variable data.” See also Attribute Data. |
Common cause | Normal, everyday influences on a process; usually harder to eliminate and require changes to the process. Problems from common causes are referred to as “chronic pain.” See also Control Charts; Run Chart or Time Plot; Special Cause; Variation. |
Checksheet | Forms, tables, or worksheets facilitating data collection and compilation; allows for collection of stratified data. See alsoStratification. |
Charter | Team document defining the context, specifics, and plans of an improvement project; includes business case; problem and goal statements; constraints and assumptions; roles; preliminary plan; and scope. Periodic reviews with the sponsor ensure alignment with business strategies; review, revise, refine periodically throughout the DMAIC process based on data. |
Cause and Effect diagram | Also known as a “Fishbone” or “Ishikawa Diagram”; categorical brainstorming tool used for determining root-cause hypothesis and potential causes (the bones of the fish) for a specific effect (the head of the fish). |
Black Belt | A team leader, trained in the DMAIC process and facilitation skills, responsible for guiding an improvement project to completion. |
Baseline measures | Data signifying the level of process performance as it is/was operating at the initiation of an improvement project (prior to solutions). |
Balanced scorecard | Categorizes ongoing measures into four significant areas: finance, process, people, and innovation. Used as a presentation tool to update sponsors, senior management, and others on the progress of a business or process; also useful for process owners. |
Analyze | DMAIC phase where process detail is scrutinized for improvement opportunities. Note that: 1. Data is investigated and verified to prove suspected root causes and substantiate the problem statement (see also Cause and Effect). 2. Process analysis includes reviewing process maps for value added/non-value-added activities. See also Process Map; Value- Adding Activities; Non-Value-Adding Activities. |
Control | DMAIC phase C; once solutions have been implemented, ongoing measures track and verify the stability of the improvement and the predictability of the process. Often includes process management techniques and systems including process ownership, cockpit charts and/or process management charts, etc. See also Cockpit Charts; Process Management A statistical concept indicating that a process operating within an expected range of variation is being influenced mainly by “common cause” factors; processes operating in this state are referred to as “in control.” See also Control Charts; Process Capability; Variation. |
Control charts | Specialized time plot or run chart showing process performance, mean (average), and control limits; helps determine process influences of common (normal) or special (unusual, unique) causes. |
Cycle time | All time used in a process; includes actual work time and wait time. |
Customer requirements | Defines the needs and expectations of the customer; translated into measurable terms and used in the process to ensure compliance with the customers’ needs. |
Customer | Any internal or external person/organization who receives the output (product or service) of the process; understanding the impact of the process on both internal and external customers is key to process management and improvement. |
Criteria matrix also known as Cause and Effect Matrix | Decision-making tool used when potential choices must be weighed against several key factors (e.g., cost, ease to implement, impact on customer.). Encourages use of facts, data, and clear business objectives in decision making. |
Cost of Poor Quality, or COPQ | A dollar measures depicting the impact of problems (internal and external failures) in the process as it exists; include labor and material costs for handoffs, rework, inspection, and other non value adding activities. |
Affinity Chart (diagram) | Brainstorming tool used to gather large quantities of information from many people; ideas usually are put on sticky notes, then categorized into similar columns; columns are named giving an overall grouping of ideas. |