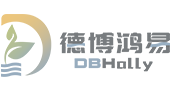
Monthly Management Tips
- Learn from experts every month for free
- Valuable information direct to your email
- Easy to read and you can cancel anytime
There are a lot of terms that are specific to Lean and Six Sigma. If you are unsure about the meaning of a term, please feel free to check our Lean and Six Sigma Glossary for a definition. If you do not find the term you are looking for, please contact us. We would be happy to answer your questions, and we may add your term to the glossary in the future.
Goal statement | Description of the intended target or desired results of Process Improvement or Design/Redesign activities; usually included in a team charter and supported with actual numbers and details once data has been obtained. |
Force field analysis | Identifies forces/factors supporting or working against an idea; “restraining” factors listed on one side of the page, “driving forces” listed on the other; used to reinforce the strengths (positive ideas) and overcome the weaknesses or obstacles. |
External failure | When defective units pass all the way through a process and are received by the customer. |
Efficiency | Measures related to the quantity of resources used in producing the output of a process (e.g., costs of the process, total cycle time, resources consumed, cost of defects, scrap, and/or waste); links primarily to company profitability. |
Effectiveness | Measures related to how well the process output(s) meets the needs of the customer (e.g., on-time delivery, adherence to specifications, service experience, accuracy, value-added features, customer satisfaction level); links primarily to customer satisfaction. |
DPO, or Defects per Opportunity | Calculation used in Process Improvements to determine the amount of defects per opportunity; number of defects divided by (the number of units times the number of opportunities) = DPO.See also Defect; Defect Opportunity. |
DPMO, or Defects per Million Opportunities | Calculation used in Six Sigma Process Improvement initiatives indicating the amount of defects in a process per one million opportunities; number of defects divided by (the number of units times the number of opportunities) = DPO, times 1 million = DPMO. See also DPO; Six Sigma; Defect Opportunity). |
DMAIC | Acronym for a Process Improvement/Management System which stands for Define, Measure, Analyze, Improve, and Control; lends structure to Process Improvement, Design or Redesign applications. |
DFSS | Acronym for “Design for Six Sigma.” Describes the application of Six Sigma tools to product development and Process Design efforts with the goal of “designing in” Six Sigma performance capability. |
Defect | Any instance or occurrence where the product or service fails to meet customer requirements. |
Downstream | Processes (activities) occurring after the task or activity in question. |
Discrete data | Any data not quantified on an infinitely divisible scale. Includes a count, proportion, or percentage of a characteristic or category (e.g., gender, loan type, department, location, etc); also referred to as “attribute data.” |
Define | First DMAIC phase defines the problem/opportunity, process, and customer requirements; because the DMAIC cycle is iterative, the process problem, flow, and requirements should be verified and updated for clarity, throughout the other phases. See alsoCharter, Customer Requirements, Process Map, VOC. |
Defective | Any unit with one or more defects. See also Defects. |
Defect opportunity | A type of potential defect on a unit of throughput (output) which is important to the customer; example: specific fields on a form which creates an opportunity for error that would be important to the customer. |