What is a Standard Work Event?
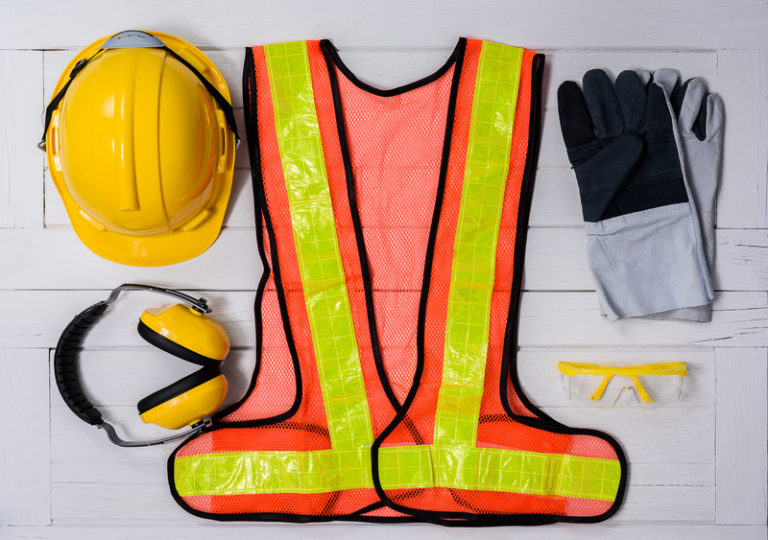
Besides being one of the most powerful tools in the lean toolbox, Standard Work is one of the least understood and seldom used. Through documentation of current best practices and evaluation of the process flow, Standardized Work provides a baseline for continuous improvement, or Kaizen.
“Where there is no standard, there can be no kaizen” – Taiichi Ohno, developer of the Toyota Production System (lean)
When solving a problem, we must first determine if a standard exists. If there is no standard, one must be created. If one exists, then it must be changed or revised. If the standard exists, but is not followed, then we must investigate the root cause of why it is not being followed.
All in all, the improvement of standard work is a never-ending process, but a critical element to any Lean Six Sigma success.
Learn More About Standard Work
The 5-day long Standard Work event is an example of a Kaizen burst, though it is specific to implementing standard work on business processes. The event ideally follows a Value Stream Mapping event, with the team gathering to carry out a Gemba walk and perform preparatory work before the event.
Aims and Elements of a Standard Work Event
The establishment of standardized work is reliant on the collection and recording of data on forms. The forms may then be used by frontline supervisors and engineers to evaluate work processes, and by operators who want to make improvements to their jobs. During the standard work event, employees find out how they can use the forms and understand why standard work is essential in making lean implementations sustainable.
At its most basic, standardized work events involve looking at four elements, namely:
- Takt Time: The rate of production required to meet demand from customers.
- Work Sequence: How an operator performs their tasks within Takt time.
- Standard Inventory: This includes machine units necessary for the smooth operation of work processes.
- Level Loading: Balancing out the workload at each station/process to maintain a steady flow and achieve customer demand
Often times, people assume that standard work only involves standard operating procedures (SOPs) or documentation, but it goes far beyond that.
Identifying The Business Case for Standard Work
A business case and problem statement is the kickoff for this Kaizen event and can be defined as the level of discrepancy between the expectations of the customer and the current processes. A business case sets the focus for the Kaizen event and should be documented, so that leadership support could be agreed upon ahead of time.
Examples of Kaizen business cases include:
- Increase in on-time delivery performance
- Reduction of inventory
- Elimination of bottlenecks
- Reduction of lead time
- Elimination of scrap
- Increased capacity
- Reduction of changeover time
- Reduction in floor space
- Improved quality
- Reduction of machine failures
Reserve a facilitator for Upcoming Kaizen Events
Set Your Goals
Your goals for a standard work Kaizen event should be measurable. The goals should also be in alignment with your company’s strategies as identified by the Value Stream Map, touching on areas such as cost, safety, delivery times and quality, among others. They need to be challenging, but at the same time, realistic.
Select The Kaizen Standard Work Team
A Kaizen team should be selected based on the work areas that are being improved. The standard work event team should consist of 2 to 6 people per process or machine, with each team also having a Team Leader or trained facilitator. Every member of the team should have been chosen for a specific specialty and may include management, who can offer a “different set of eyes”, internal or external suppliers, customers, change agents, maintenance and subject matter experts (SMEs).
Collect Your Baseline Data
The next phase involves collection of baseline data which will assist in setting of baseline goals. Examples of commonly collected information includes: Takt time, cycle time, space constraints, customer satisfaction, lead times, safety/ergonomics, distance travelled, defects, visual measurement, 5S and current standard work processes. The team leader or facilitator uses the information and input from team members to produce a process map, spaghetti diagram, or value stream map of the problem that is being addressed.
Support Continuous Activity
During the event, observations and analysis are performed to determine the best way to establish flow, pull and improvements in quality, such as:
- Setting up a workload balance sheet
- Leveling workload across workstations
- Separating of value added tasks from non-value added tasks within work combination sheets
- Calculation of standard work in progress
- Redesign of workspaces to improve flow and reduce waste
- Validating the effect of new layouts and work processes
After improvements are tested out and verified, and metrics improved, then new standard work should be established.
Conclusion
Standardized work adds an element of discipline to the workplace improvement culture. This is something that is often overlooked, but is essential if lean is to succeed. It is also an excellent learning tool which promotes problem solving, supports audits and includes team members in the continuous improvement effort.
For more information on our Kaizen Events & Six Sigma courses and services, please visit 6sigma.us.