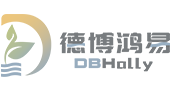
Monthly Management Tips
- Learn from experts every month for free
- Valuable information direct to your email
- Easy to read and you can cancel anytime
“6Sigma.us” team of Lean Experts and Master Black Belts have provided event facilitation globally for over 10 years with clients in all business segments and industries.
We realize that each event is unique and may be very focused or very broad in scope, which will vary the length of the event. It also requires different preparation, change management, data collection and facilitation needs. The key to a successful event is the preparation and planning before the event using a cross-functional team. Included in this price is coaching and mentoring prior to the event, using the phone, email & virtual meetings (GoToMeeting).
Having an outside perspective, someone who is independent of your processes and business can be a huge advantage to using an external consultant. We aren’t biased by what has been done in the past, and we can bring our experience from multiple companies and industries to assist the team. We realize it can take a lot of effort to plan an event, and we can walk you through those steps, so that your kaizen event gets completed, and gets the impact you desired. You don’t have to research what to do next or hope that you did everything correctly. We will coach and mentor you so that you can run your own events in the future (by providing a co-facilitator that we can work with).
Prior to the Kaizen Event, we will help you with the following tasks to ensure a successful event:
Please contact us to discuss the scope and deliverables of your kaizen event, so we can help you determine the duration and estimated cost.
During the kaizen event, we will assist with the following activities:
Reserve a facilitator for an upcoming kaizen event
Duration: (1-3 days)
Ideal for understanding the current state, ideal state and future state of a process. Not as complex or as expansive as a Value Stream Map (informal mapping with less data collection and preparation). Ideal for mapping processes within a department or small team.
Duration: (3-5 days)
Ideal for mapping the flow of material or information from customer request to customer delivery, spanning multiple departments and organizations. A great approach when you are just starting out, so you can decide which areas should be worked on first. Requires considerable preparation work to gather data for each major process step prior to the event. During the event, training is provided, go and see (gemba walk) is conducted, then Current State VSM is created. Wastes and opportunities are identified on the map, and an Ideal state map is developed. A future state map (6-12 months in the future) is developed, based on the gaps from Ideal State and Current State. End result is a Future State VSM, with a list of opportunities with assignees and due dates for improvement, in order to move the process closer to the Future State.
Duration: (3-5 days)
A working session, where the purpose is to complete a specific set of tasks by the end of the event. There is a limited amount of analysis, most of the time is spent implementing the changes, and validating that they work. These are ideal for bringing a team together to make significant progress on a task that has been dragging on too long. Unlike a mapping event, 80% of the actions are completed during the event, with the remaining 20% completed within the next 30 days.
Duration: (3-5 days)
Interested in getting immediate results and benefits in an area or department, without having to learn a bunch of Lean terminology or tools? 5S events are a great way to get work spaces organized and decluttered, and the results are immediate, which builds excitement from the team to take on future improvements. This goes beyond “spring cleaning,” as we walk your team through the 5 steps (5S) for organization. At the end of the event, the team will be through the Sweep, and will have some standardization in place, along with a draft of the sustainment plan.
Duration: (3-5 days)
Ideal for getting your process equipment back to ideal working condition, and setting up processes to maintain it, so there is less risk for downtime. We start by identifying the key equipment or area to focus. Next, we break down and inspect the entire machine, and get it back to “optimal working condition.” Data systems are put in place to determine when equipment isn’t working properly, and the top drivers of downtime are investigated and continuously improved. Finally, preventative maintenance is implemented to reduce degradation of the equipment.
Duration: (5 days)
This is a type of kaizen burst event, but specific to the implementation of standard work on a process. Ideally performed after a VSM event, the team gathers to review the process, conduct a gemba walk, and review the preparation work collected prior to the event. The team goes through a series of steps, including: Calculating takt time, creating workload balance sheet, completing standard work combination sheets to separate value added from non value added tasks, performing level loading of work across the stations, defining work sequence, calculating standard Work In Process (WIP), redesigning the space to optimize flow and reduce waste, implementing the layout change, and validating that the new processes and layouts are working properly.
6Sigma.us is offering the following options for Lean event facilitation and consulting support:
On-site support during the preparation stage is also available at the same rates.
For example, if you would like a 5-day VSM event, and 2 days of on-site preparation support, the cost would be $10,000 for the event, $5000 for the preparation work, plus travel expenses for both trips.
Reschedules and cancellations should be made at least one week in advance and may require repayment of lost or extra travel expenses.
To discuss your specific event needs, contact us.