Six Sigma and DMAIC in Focus: M – Measure Your Six Sigma Project
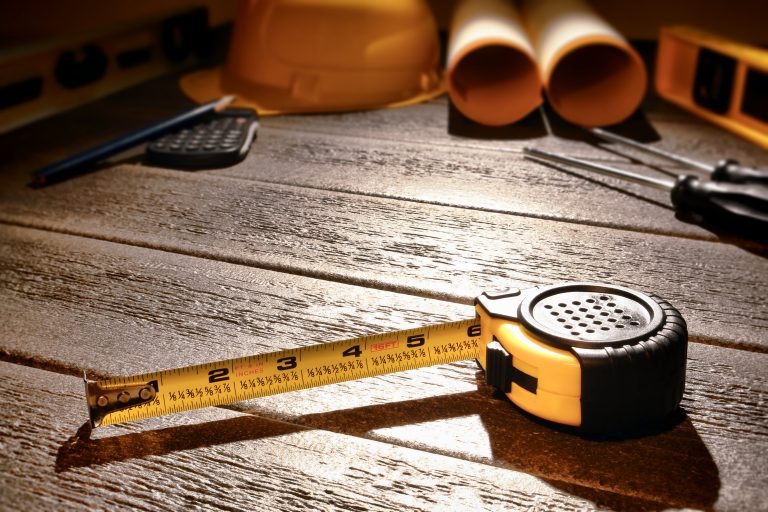
This article is the second part in our series on the principles of Six Sigma, focusing on Measure within the DMAIC framework. You can find the rest of our series here.
Yesterday we started our series on DMAIC in focus with a deep-dive into Define. Today we take a more measured approach and will give you an overview of Measure. What is it, and how does it contribute to a successful Six Sigma project? You’ll find out here. We have also provided you with a swiss-army knife measure toolkit, so you can get right to work!
What is Measure?
You’ll get no prizes for using a little common sense here (we did mention it yesterday) – the second stage in the DMAIC improvement cycle is Measure. It takes aim at your business progress and current baselines to inform potential and proposed improvements.
Measure means exactly that. It calls for the collection and collation of data, enabling you to establish baselines (metrics) to be used for process improvement. Baselines are powerful, as you you can objectively prove the improvements made at project close.
You can then see the effects of the DMAIC cycle in comparison to pre-improvement performance levels. Your project team can decide on further areas to be improved and measured at this point. You can also develop criteria and suggest a methodology to help. Good data is the crux of everything DMAIC does and leads you to make better decisions. Better decisions, in turn, provide continued success in your post-DMAIC activities.
Your Measure Toolkit
The Measure step involves a lot of documenting. It’s necessary, but we often get asked if there are tools to help visualize the high volume of data it produces. The good news is, there are a lot of tools out there! We’ve put together a few of our favorite, and essential, tools to help you, so you can stop worrying and start measuring:
- Trend charts – Trend charts are a simple tool for measuring long-term data. Often, when analyzing a problem, taking the longer view gives some interesting results. You can apply simple psychology here, as people tend to become accustomed to their surroundings. Trend lines reveal a general pattern of change within your business, so don’t underestimate them!
- Basic Pareto charts – A Pareto chart allows you summarize and display data that will highlight differences between the groups of data presented (i.e. the frequency of certain customer questionnaire responses).
- Process flow charts – Process flowcharts need no introduction. They are visualizations of business processes. You would be surprised at how many businesses have processes ‘in their head.’ This leads to a lot of ad-hoc processes, and therefore inconsistent implementation. When in doubt, draw it out!
- Gage R&R – This stands for Gage repeatability and reproducibility. Use it to measure the amount of variation that occurs. Typically, there are two sources of variation, the variation of the process itself and that of the measurement system used to assess it. Gage R&R lets you see the differences between these two categories. The aim? Reducing the variation in your measurement system.
- Process capability measurement – You can use this tool to, among other things, analyze input characteristics. They key is, they have to be measurable, so keep that focus. Doing this will illustrate normal distribution, process mean, and standard deviation. You can also use Control Charts to analyze whether a process is in statistical control or not. Simple really.
Conclusion
You can use Measure to shed light on areas that need addressing from an early stage. It also provides clues as to how to move forward and gives legitimacy to your project. It gives your team the hard data they need, which is especially relevant when providing insights to identify further and combat critical problem areas.
Contact us at 6Sigma.us and find out how we can positively change the culture and operations of your manufacturing unit. We offer Green Belt and Black Belt training programs, as well as a Master Black Belt program.