How to Avoid Complacency and Continually Improve with Six Sigma
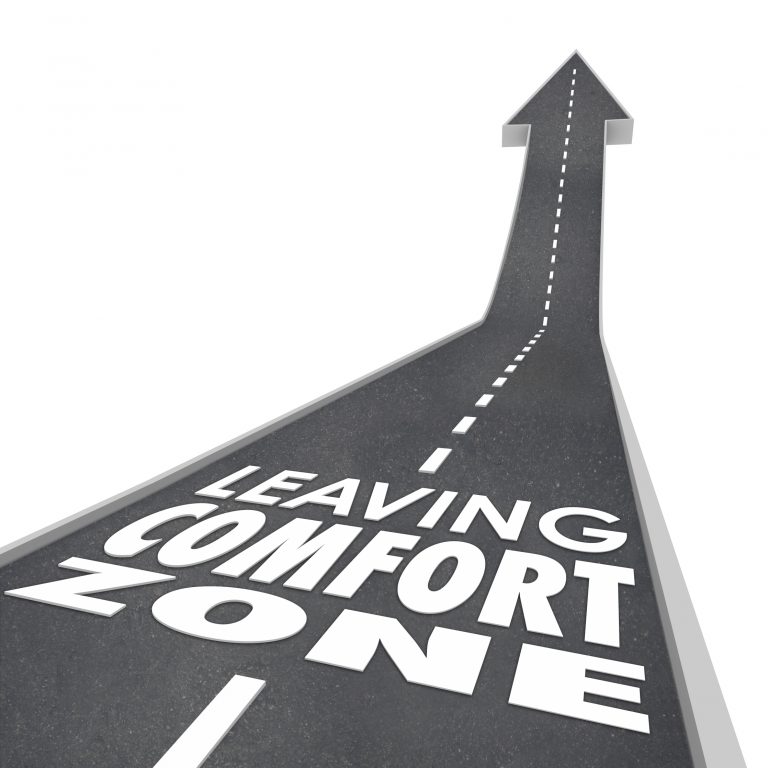
Complacency is an epidemic. It kills productivity and can negatively affect your performance. Studies have shown that complacency comes from a lack of engagement, and affects up to 70% of the US working population. This means around three-quarters of American employees are not fully committed to their everyday workplace tasks! As an employer, this should concern you, as employees who are unengaged contribute to slow production processes, not to mention the loss of profit.
Don’t let this happen to your company! To combat complacency and cultivate continual process improvement in your company, Six Sigma is the strategy for you.
Killing Complacency for Good
Complacency arises from a lack of motivation and poor engagement. As an employer, it’s your responsibility to properly motivate your staff to get the job done. There are various ways by which you can achieve this:
- Offer incentives. This can be either a financial or material incentive linked to individual performance or through opportunities for advancement and progression. If your employees have something to work towards, they will do their best to achieve it. This will also teach them to seize further opportunities and ensure they remain motivated for the future.
- Provide constructive feedback. Any criticism should always be constructive. Be sure to recognize where someone has done well. Reward their hard work. Acknowledge how important their role is in the company, especially for employees who have worked for you a long time. Be careful to avoid favoritism.
- Welcome their feedback. Be sure to welcome and take an interest in what your employees have to say. Look to them for ways to improve the company, to make their work lives more enjoyable and more engaging. This will benefit the entire company and not just the individual.
- Establish a team spirit. Have faith in all your employees. Help them to see themselves not just as a gear in the machine, but as a vital organ without which the company would fail to function. Employee of the week, month, or year awards can help encourage friendly competition and better results from your staff too.
Using Six Sigma for Continuous Improvement
Six Sigma is a team effort that requires everyone give their best to solving problems that affect production. Complacency can cause a company to become sluggish and unproductive. The above tips should help you eliminate it for good. Remember, firstly you need to draw up a business case. Then you can cultivate a strong change management plan.
A business case is a document that justifies and illustrates the reasoning behind a project. It should outline why Six Sigma is necessary for your company and what you hope to achieve using it.
Similarly, your change management plan should detail how you intend to help your teams make the transition to Six Sigma, how you will redirect your resources to aid your plan, allocate new budgets and reshape your production stages according to Six Sigma methodology.
Adopting Six Sigma philosophy takes time. You will learn how to recognize, isolate and reduce variation in your production line. Remember, if a company operating at only three sigma produces approximately 67,000 defects per million, operating using Six Sigma will reduce this to as little as 3.4 per million. You can achieve this for your business too.
Don’t let complacency and variation hold your company back. With Six Sigma, there’s nothing to stop you achieving success!
Stop by and contact us at 6Sigma.us and find out how we can positively help you plan and change the culture and operations of your organization. We offer Green Belt and Black Belt training programs, as well as a Master Black Belt program.