Benefits of Toyota Production System (TPS)
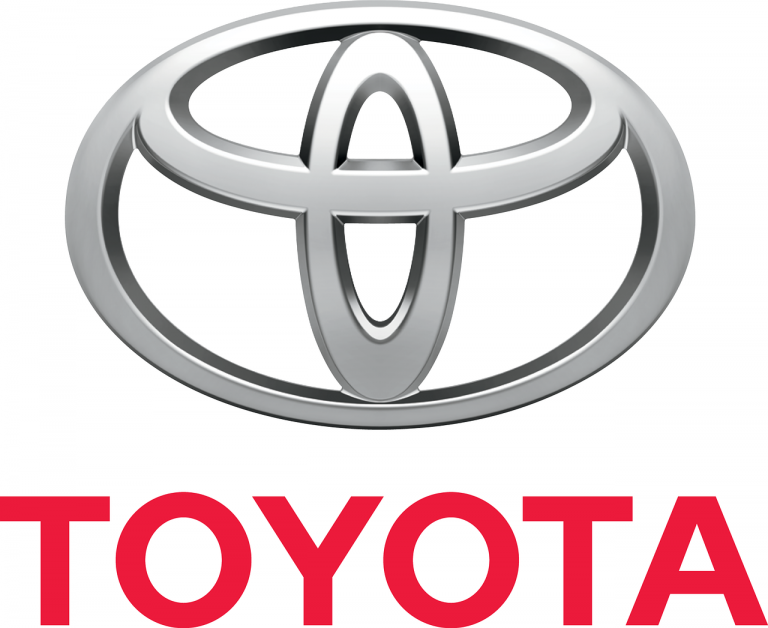
Toyota production system (TPS) is like a super charged Lean Six Sigma program. All the proven and intelligent methodologies of conventional TPS Six Sigma have been charged with immensely motivated team associates.
TPS is the outcome of such powerful Lean Six Sigma team associates sigma, which leads to high performance culture and lets employees to know their full strength. It also bestows creatively, while the firm gains from increased, profitability, market share, productivity, and high customer satisfaction.
Toyota Motor Corporation created this Six Sigma system to offer best quality, low priced and shortest lead-time by eliminating wastes. Generally, the Toyota production system (TPS) consists of two pillars such as Just-in-Time and Jidoka. People often illustrate it with the name House. TPS is improved and maintained through loops of consistent work and improved quality.
Elimination of Waste has several forms such as material, idle equipment, time, and inventory. Most organizations do waste about 70% to 90% of their existing resources. Hence, TPS emphasizes the detection of such waste followed by certain Six Sigma tools and systems to eliminate it.
Learn More About Our Lean Six Sigma Training Programs
Inventory is one such largest waste. It demolishes capital, become outdated and consumes both space as well as workforce. At times, it also hides other kinds of wastes. Almost each defect or difficulty makes a need of inventory. Thus, inventory is an outcome as well as evidence of overall manufacturing effectiveness.
TPS’s Six Sigma
Below discussed are some of the TPS’s (Toyota production system) Six Sigma strategies:
1. Decreased setup times: All setup procedures are wasteful, since they do not add any value and tie-up labor and equipment. By handling procedures, using carts and training employees to carry out their own setups, Toyota has managed to slash setup times from month to hours, and even minutes.
2. Minimum Production: Manufacturing things in bulk batches sometimes may lead to huge setup costs, capital cost, large inventories, unlimited lead times and huge defect costs. As Toyota has found this ideal method of minimum production to make setup inexpensive and short, now it has become possible for them to manufacture various things in smaller quantities.
3. Workers Empowerment and Involvement: Toyota ordered their employees to form teams and offered them the training and responsibility to carry out certain specialized tasks. Team members were also given the task to repair equipment and take care of internal factory work. Every team has a head, who also acts as one of the prospective employee in achieving specialized task assigned to them.
4. Dealers Participation: Toyota treats its dealers as company partner, as integral part of TPS (Toyota production system). Dealers are also well familiar with ways to decrease setup times, defects, inventories and machine breakdowns and take responsibility to render their best possible outcomes.
Overview
The Toyota Production System blends attitude, notion and specific techniques into a structured socio-technical Six Sigma system for manufacturing. Gradually, this Six Sigma system spread around Japan and finally to the West, and started gaining other names and variations. Toyota itself was not having any name for its manufacturing strategy until the 1970’s.
Just in Time, Stockless Production, World Class Manufacturing, Demand Flow Technology and several other terms are mostly the variations of Toyota’s Six Sigma system. Lean Manufacturing, given by James Womack, is a name that appears to sticking very firmly.
When everything has been well done, TPS fetches order of great improvements in inventory, material handling, scheduling, and customer satisfaction. The payoff to dealers and shareholders is important and well acknowledged.
The TPS’s Six Sigma system has been doing well for Toyota, its dealers, and several other companies. Often, Six Sigma is an ideal starting point, but is hardly a substitute for a personalized and well-throughout manufacturing strategy.
Contact us at 6Sigma.us and find out how we can positively help you plan and change the culture and operations of your organization. We offer Six Sigma Green Belt and Six Sigma Black Belt training programs, as well as a Master Black Belt program.