Disrupt the Status Quo: Practical Six Sigma Thinking!
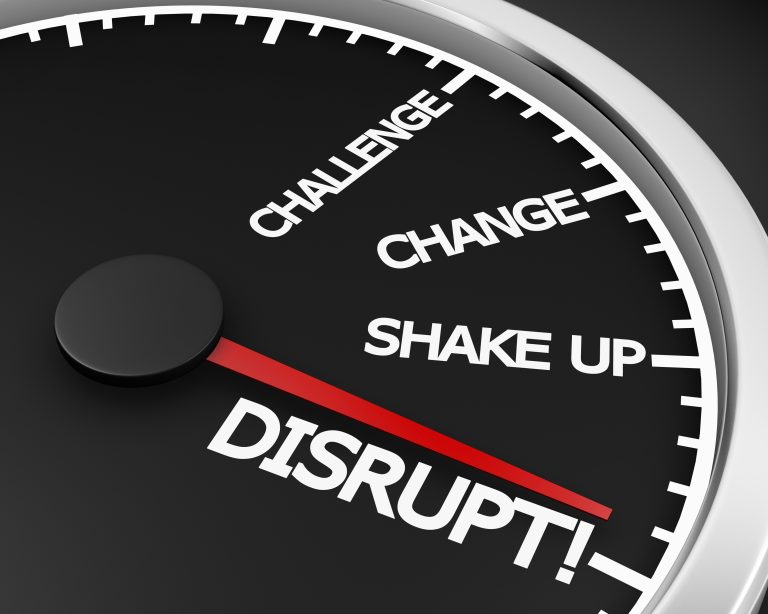
You will find Six Sigma principles the world over. For many businesses, Six Sigma is a highly transformative strategy for process improvement. Using key Six Sigma principles, you can achieve the same for your company.
Not only does Six Sigma provide ways by which to bring about improvement, but it can also help disrupt the status quo, knocking back your competitors so that you can reap the rewards.
We will teach you about the key principles behind Six Sigma methodology and how disruption can be used to your advantage.
What are the Key Principles of Six Sigma?
If you are to use Six Sigma principles most effectively, it’s important to understand just what they are and what they mean. Rather like Kaizen, Six Sigma can be broken down into these seven easy steps:
- Focus on your customer(s). Greater understanding of customer needs and potential needs ensures your company-customer relationship is successful.
- Recognize and understand the value stream. Recognize problems by breaking tasks down and knowing how tasks get done.
- Manage, improve, smooth flow. Control of flow is key to recognizing opportunities for waste elimination.
- Eliminate waste – Waste is detrimental to your company’s success.
- Regulate based on factual data and minimize variation. Hard facts help you make the best decisions. Variation can lead to losses over time.
- Encourage involvement in your employees and equip them appropriately. It’s a team effort that requires total participation.
- Carry out improvements systematically. Six Sigma isn’t a one-use fix-all solution. It is a gradual process that takes time but achieves the best results.
How to Use Six Sigma to Disrupt Status Quo
Six Sigma’s data-driven method to improvement means you can get the upper hand over your competitors. Tools for minimizing defects are useful here due to Six Sigma’s reliance on hard facts and quantitative data. This approach sets you up from the beginning to make beneficial decisions based on accurate observations. Overall, and we cannot stress it enough, this is the key to success.
We find that many businesses that don’t use Six Sigma almost always rely on alternative and inferior improvement methods like TQM. You will find Six Sigma often scores higher for quality improvement than techniques like TQM, which bases achievement on quality level. While this may help create higher rates of efficiency, in the end, TQM ultimately lacks the consistency for quality improvement. Unlike a lot of companies, you will continuously eliminate waste that other companies will be unable to access and identify. You can streamline production by removing redundant processes, and carry out the improvements in a methodical way.
Using the principles above almost always gives you a head start over your competition. You can achieve faster, more consistent improvement in quality, production processes, efficiency, and productivity. Furthermore, when used in conjunction with similar complementary improvement philosophies such as Kaizen and Lean manufacturing, you can throw your competitors off their game. Most of all, using Six Sigma principles allows you to take advantage of the market and use it to your advantage. The strong focus on the customer and your relationship with them is one of Six Sigma’s many unique features.
Contact us at 6Sigma.us and find out how we can positively change the culture and operations of your manufacturing unit. We offer Green Belt and Black Belt training programs, as well as a Master Black Belt program.