DMAIC Approach in Lean Six Sigma
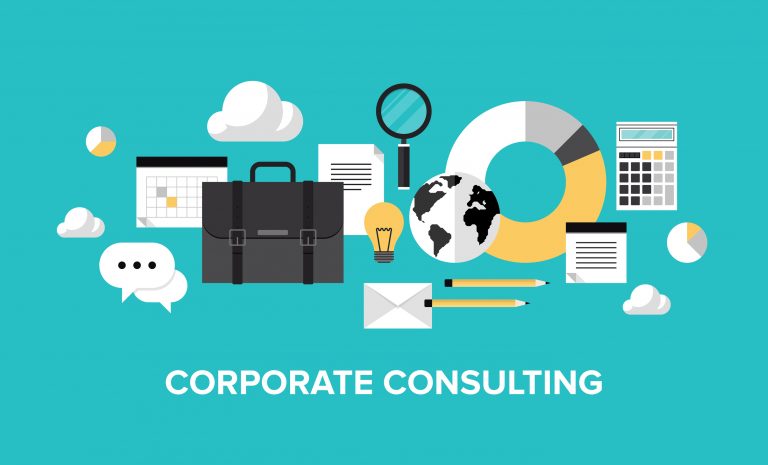
Six Sigma Concepts are used to improve the effectiveness and efficiency of business performance. The statistical representation of Six Sigma describes the performance of the process. A process is said to achieve Six Sigma only if it doesn’t produce more than 3.4 defects per million (DPM) opportunities. Six Sigma focuses on process improvement and reduces the variation of the process. Six Sigma is driven by a DMAIC approach that identifies, measures, analyzes, improves and sustains the process. DMAIC is a cycle used to eliminate the defect or improve the opportunities in the process for business improvements through five main steps: Define, Measure, Analyze, Improve, and Control.
What is DMAIC in Six Sigma?
DMAIC Methodology is a data-driven quality strategy utilized for process improvement through integrating a Six Sigma quality initiative. Define is the initial stage of DMAIC methodology. It defines the CTQ (critical to quality) issues and the core business process involved. In detail, it explains the customer requirements, expectations of the customer, project boundaries, stop and start the process, a process flow of the process.
The performance of the core business is measured in Measure stage. Data collection plan is scheduled in the process to determine the types of defects and metrics in the process. Based upon the collected data gaps between the current and goal performance and process variation is identified. Further, analyze is performed to determine the root causes of defects and opportunities for process improvement. A potential solution is identified to eliminate or reduce the defects in the process. The implementation plan is implemented at Improve Phase. Control Phase includes standardization and documentation of the new process. It creates a plan to monitor the process and ensure the process performance is in control.
How DMAIC perform as an approach to problem-solving?
DMAIC is a roadmap used as the problem-solving method for process or quality improvement.
DMAIC method differs from conventional problem solving since it belongs below steps during problem-solving:
— Define
- Define customer expectations
- Define impacted business processes
- Define project boundaries
- Define metrics
- Define Team members, Project Leader
— Measure
- Data collection
- Measure process
— Analyze
- Analyze gathered Data
- Identify gap between existing and goal performance
- Analyze the cause for the gap
- Decide on the processes to be improved
— Improve
- Identify potential solutions
- Pilot Study
- Test
- Evaluate proposed solutions
- Develop implementation plan
— Control
- Implement process
- Develop Standing Procedure
- Develop Control Plans
- Train staff on new process
How to apply DMAIC Steps to Continuous Improvement Projects?
Six Sigma is not just going about solving day-to-day problems but identifies the cause of the problem and provides the potential solution to solve and control the problem.
Below series of common sense questions on each process could lead to solving the problem in a statistical method:
Define – What is the outcome to be measured?
Measure – What is the current performance of the process that is measured?
Analyze – What are the real causes? What is really causing the problem?
Improve – How can the real cause be eliminated from the process or the size of the problem can be reduced?
Control – Did the process improved?
What are the controls placed to sustain the improvements?
Tools used in DMAIC Approach:
Define:
- Develop Project Charter
- KPIV – Key process Input variable
- Voice of Customer
Measure:
- Create “As-Is” Process map
- Control Chart
- Capability Analysis
Analyze:
- Fishbone
- Failure Mode and Effects Analysis
- Scatter Plots
- 5-Why analysis
Improve:
- Brainstorming
- Design of Experiments
- Pilot-Planning
Control:
- Mistake Proofing
- Standard Operating procedure
- Control Plan
- Audit Plan
- Training Plan
For more information on our Six Sigma courses or services, please visit our course schedule.