Getting Started with Lean Six Sigma
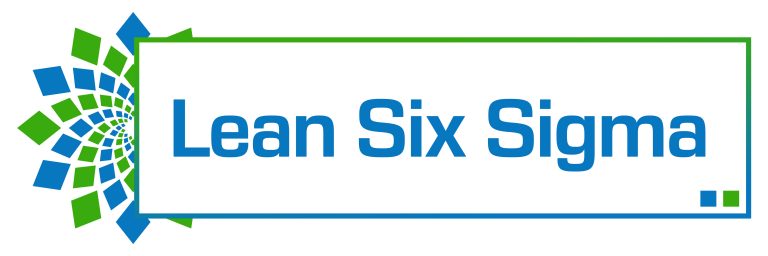
Lean Six Sigma is a customer-focused business enhancement strategy. It involves utilizing a set of management techniques designed to improve business processes by greatly reducing the probability of errors or defects.
Most companies are in business for two reasons:–
1) to provide excellent customer services, and
2) to ensure a profitable venture for all involved.
Lean Six Sigma allows you to deliver accelerated results that satisfy both these goals.
For optimum deployment, a burning platform first needs to be created. In other words, there must be a valid reason for Lean Six Sigma to be put into place, otherwise, it won’t have much effect. If your company is suffering from high quality losses which account for a high percentage of costs, this is an acceptable reason. If your competitors are pushing you out of your market by 15 percent each quarter, this is also a valid reason.
Secondly, resources must be organized and utilized properly. Staff, materials, technology, property must be appropriately sourced and selected. Potential resources vary, and it can be difficult to know which is right for you. If a piece of machinery has limited functionality, even though it costs less, it could affect your later performance significantly. With Lean Six Sigma comes greater efficiency and profitability, as waste takes up valuable time, while adding nothing to the end-product. Similarly, if an applicant for a customer service role doesn’t seem a good fit, then you should consider other potential employees. Your resources must be cooperative and functional, as Lean Six Sigma requires a collaborative team effort from everyone and everything involved.
Thirdly, one or more staff members must be trained in Lean Six Sigma strategy and methodology. Lean Six Sigma is a global brand, and it is not difficult to find quality training. The more you invest, the more you get out, and by training team members via Yellow Belt, Green Belt, and Black Belt training, you will have dedicated assets on your side to ensure your Lean Six Sigma lasts a lifetime. After you have your resources in place and all appropriate training has been concluded, it should be your organization’s priority to: take note of customer demands, recognize critical-to-quality conditions, and make sure your Lean Six Sigma practices are directed towards company goals. Establishing ownership is vital, as your staff require a leader, someone committed, accountable, and engaging to follow. Without a clear hierarchy or “boss” to look up to, productivity, performance quality, efficiency, will all start to slide. It is your responsibility to ensure this doesn’t happen.
Measurements are important to Lean Six Sigma, as it enables you to locate problem areas and conceive improvements. Cost-of-quality is important, which is why efficient strategies need to be implemented to eliminate waste. This will bring in data quickly, allowing you to remove lagging indicators and improve leading ones. Hierarchy helps sustain program momentum, as poor governance and lack of guidance can be detrimental. Regular meetings, clear schedules, and review sessions all help create a best practice sharing forum that will prevent and deter your employees from losing direction.
Finally, as part of your managerial duties, it’s important to recognize and show appreciation for your team’s contributions. Reward them for their hard work, show your enthusiasm for what they are doing. This will motivate them, and improve their performance and innovation, as time progresses, which will in turn benefit the company.
Lean and Six Sigma methodologies are hugely beneficial alone, but when combined, the rewards are maximized. Using Lean Six Sigma, many companies around the world are optimizing their business processes to deliver the best services for consumers, with high levels of profit. You can do the same.
You can go to https://www.6Sigma.us/six-sigma-training.php to learn more about our training solutions.