Lean Process Improvement Techniques – Dummies Guide
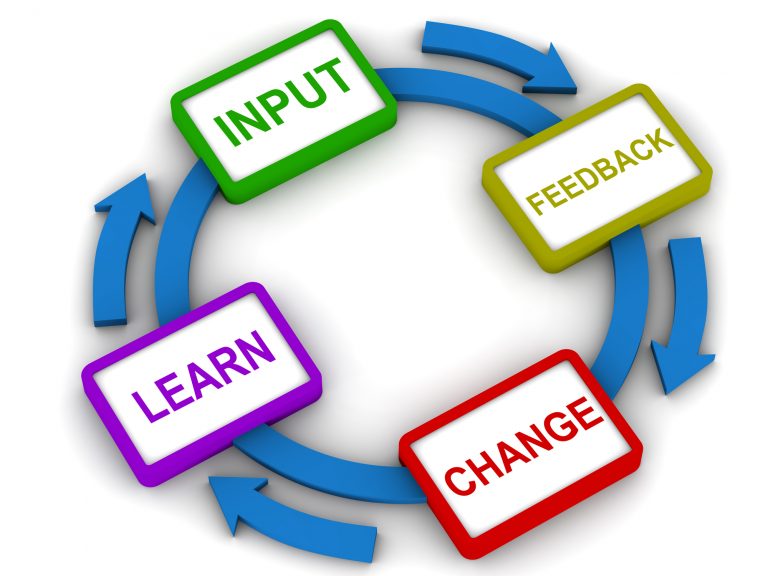
Let’s look here at techniques for achieving Lean process improvements. When you begin to address a problem or improve a process some good techniques to get off to a good start include:
• Determine the problem and process to address
• Use a project charter
What is a project charter? It is a document you create to explain your goal. Most groups find that simple is best with this charter and one page can work. The charter can include:
• 1 or 2 sentences that describe a problem, for example, we have over 1000 screws stored and keep getting more automatically
• a description of a goal, for example, we want to keep a smaller inventory of screws
• a description of the scope, for example, we are looking at production line #3 only
• a description of the result, for example, we want to store 100 screws and order more when we get a new order
You can also describe who is involved and what are the barriers to achieving the goal. Keep in mind the goal should be SMART or:
• Specific
• Measurable
• Achievable
• Realistic
• Timely
Move on to the measurement phase: After you determine the problem and goal, the next step should involve measurements and data.
Here are some techniques you can use in this phase:
• Include the people who do the work
• Look at all problems with the process
• Write down specifics such a how long a process takes and how much it costs
Go on to analyze: In this phase you are looking at what is causing problems and more specifically the root causes. You do not just look at the symptoms such as we have too large an inventory of screws. You look at the cause, for example, we use an automated system that gives us new screws every week.
Generate solutions: You can think now about how best to solve a root problem. If the problem is that your automated ordering system causes you to have too much inventory, you will have to ask about how much the cost is to solve a problem with a specific solution. For example, if we want to order screws without using the automated system, how much will it cost to do that.
Implement your solution: There are some best practices here and they include:
• Make solutions specific and not vague
• Define who is to take the action
• Be sure everyone involved knows exactly what to do
• Set dates that are realistic
• Make sure project leaders get feedback from those doing the work
Evaluate: Make sure you evaluate the goal statement and solution. If the solution is a good one be sure you communicate what the change is and document it.
Getting rid of waste: In addition to the process evaluation we just described, Lean takes into account how best to get rid of waste. Here are some sources of waste as defined in part by TaiichiOhno in a Toyota context.
• Inventory
• Transport
• Motion
• Waiting
• Overproduction
• Processing problems
• Defects
• Producing what the customer does not want
With inventory issues we can see, for example, a problem with too much inventory where you store either too much finished product for customer requests or too much raw product that you need to make the product. With transport problems you move products that you do not need to make the final product. Motion problems can involve equipment or people moving more than is efficient. Waiting problems can involve production interruption during shift changes. Processing issues can mean poor product or process design.
Looking at these issues for problems and implementing continuous solutions is the Lean approach.
Let’s review:
We looked at some of the basics of Lean to include a process where you carefully define a problem then go on to solve it effectively. We also looked at areas where there could be waste as removing or eliminate waste is a key concept in Lean.
So why wait, register today for your Six Sigma requirement. We look forward to seeing you in our upcoming session near you!