Six Sigma Calling: 9 Ways to Improve Call Center Quality
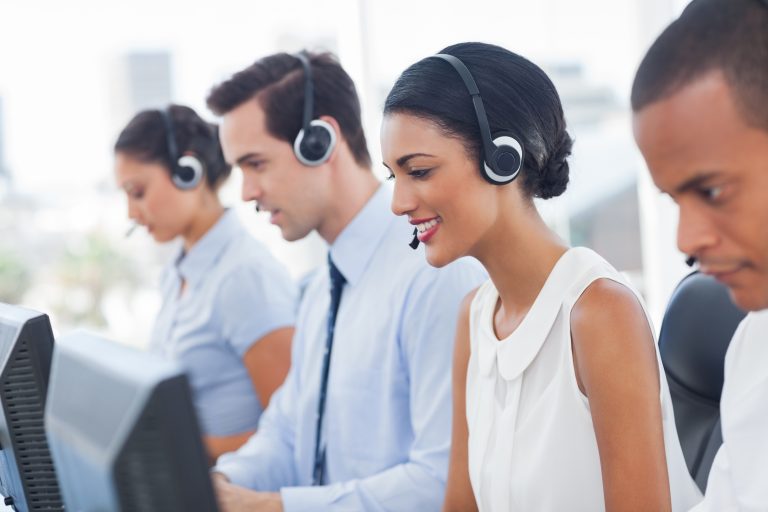
You might not associate Six Sigma and call centers right away, and we wouldn’t blame you! However, they rely on efficient processes, and high quality control, to maintain optimal results. This makes it the perfect environment to use Six Sigma, maximizing results and upholding quality. Read on and learn how Six Sigma principles can be used to increase call center quality.
Click Here To Know More About Six Sigma Certification And Training
Using Six Sigma in Call Centers
You can increase satisfaction in call centers by effectively using Six Sigma principles. Instead of focusing on individual people, take a holistic approach to the entire center. Both Six Sigma and Lean are heavily invested in teamwork, after all, which is essential to maintaining good results for critical-to-customer characteristics. These days, a lot of centers incorporate some aspects of Six Sigma, using quality programs to evaluate their calls per customer calling patterns and align them to customer feedback.
We’ve put together 9 ways to use Six Sigma to improve call center quality:
- Check-sheets. Rather than check-sheet requirements making assumptions about what customers want, they should be completely based on customer voices. It’s always better to let customers make clear for you what they want, as opposed to trying to figure out what you think they might want. This method is useful as it allows you to ascertain customer demands from those making them.
- Calls. Don’t waste time tracking a specific quota of calls each day. You’ll get far better results using random samples. It helps to diversify the overall customer exposure.
- Quality checks. Instead of carrying out quality checks monthly, it is better to perform checks daily, and report the accumulated results at the end of the month. This can give you a more precise idea of potential problem areas that may need attention more quickly than otherwise.
- Quality scaling. Rather than reporting quality results on a percentage-based scale, use line graphs and Six Sigma tools like Pareto charts to help you track trends.
- Root Cause Analysis (RCA). RCA is one of Six Sigma’s strongest, most reliable tools. You should invest significant time and effort here. You can devise methods using Six Sigma to eliminate root causes easily. Other useful tools include data verification and stratification.
- Focus. Instead of placing focus on individual employees, look at the big picture. You should focus on the processes themselves, i.e. calling patterns, conversations, data collection, as well as the whole department.
- Evaluation methods. Standardize your evaluation methods to prevent inefficiency and anomalous results. If methods vary between analysts, your total dataset will be unrepresentative, even invalid due to the lack of consistency.
- Training partnership. Define your training partnerships clearly, and base it on results from quality evaluations. Employee education should be at the forefront of your training schemes.
- Maintenance and updates. You will maintain quality by completing regular maintenance and updates. Maintenance should follow a discernible plan that aims to cultivate further improvements over time.
Stop by and contact us at 6Sigma.us and find out how we can positively help you plan and change the culture and operations of your organization. We offer Green Belt and Black Belt training programs, as well as a Master Black Belt program.