Step-By-Step Guide to VSM – Value Stream Mapping
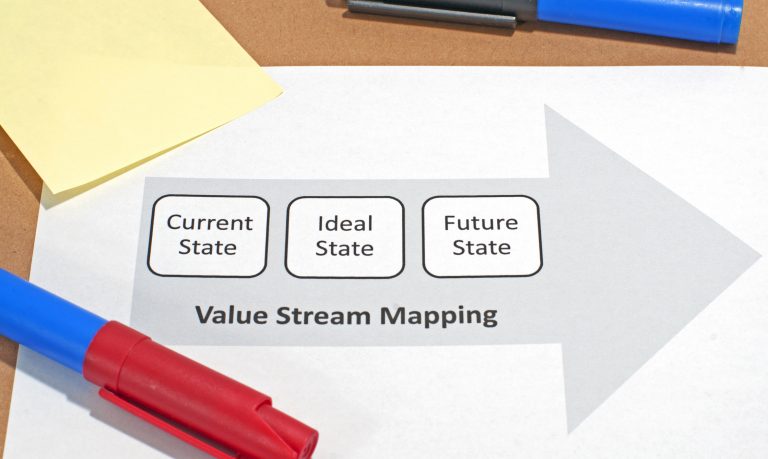
When people that don’t fully grasp process optimization systems think about the topic, they often mistakenly pay the most attention to cutting out the unneeded parts. Obviously this is a gross oversimplification, when it comes to methodologies like Lean Six Sigma, and it places the emphasis on the wrong indicator. The most important goal of this approach to business operations is creating and retaining value. The emphasis is on achieving efficiency and value. While cutting out some unnecessary expenses might be a part of it, it’s a means, not an end.
And since value is such an important metric, it’s important to have a way of visualizing and understanding the creation of value in a tangible way. Value Stream Mapping (VSM) is a visualization tool that facilitates that. It comes from the Lean methodology, and its function is to show the process the way it currently is. Followed by how it should be. The best way to understand it is to learn how to do it step-by-step.
Step 1: Preliminary Research
Before approaching any task or topic, one should devote some time to preparation and such is the case with Value Stream Mapping. So before starting the actual process of mapping, you should arm yourself with the data that is easily available. Make sure you have access to and familiarity with as much product data for your organization as possible without making a burden to yourself.
You need this because you need to identify the product or the product family that you are going to be mapping and subsequently improving. Data about volumes, turnover and margins is important since it makes a lot of sense to start your optimization efforts where they will have the highest impact which is the products with the highest values for some or all of those metrics.
Step 2: Create a Product Flow Chart
After you have selected the product or product family to create a VSM for, you should start mapping out the operational flow it goes through while moving through your organization. The best way to approach it is by starting with the boundaries.
First you need to identify how the process starts, what or who triggers it and how. Identifying who triggers is and what value are they looking to extract after doing so is paramount. Most of the time the agent will be the customer, but sometimes it might be the last step of another process, a member of the team or an external agent that is not a customer per se.
Then you should identify how the process concludes. Besides being the end of the activity, the last step of map would also include the value that the agent that started the process is supposed to be extracting in one way or another.
After the boundaries are clear it should be easier to map out all the steps that lead the product from start to end. The process steps should have information about the various stages the product goes through and one step should correspond to one operation.
Step 3: Enhance the Flow Chart with Additional Layers of Data
Besides the actual operations, it’s essential to inscribe a lot of additional information into your map for it to be as useful as possible. Time, resources, frequencies, volumes, customer demand and all important metrics and should be reflected on your representation of the process. Additionally, it’s important to map not only the product flow, but also the information flow. How requirements, specifications and demands are communicated within and without the organization is essential for full understanding of the process and usually lends itself to a lot of improvement and optimization.
Step 4: Get Your Hand Dirty
As the first 3 steps so far have been mainly theoretical, it’s very important to continue and test your VSM in practice. Get involved and observe the operation flow in practice and compare your empirical observations with your chart, making all the necessary adjustments. With this step you are ready with the “As Is” part of your VSM which reflects the current state of affairs.
Step 5: Future State
After you have gathered the all the information about the current process and have it mapped out in a comprehensive way, analysis becomes much easier and you can see the big picture. This means that you can now spot bottlenecks, inefficiencies and waste and think of ways to improve the current process eliminating the problems discovered. Doing so will lead you to create a second version of your Value Stream Map that is going to reflect the process as you would like it to be or in other words – its Future State.
Step 6: Implementation
After having understood and mapped out all the data available, the current state of affairs and the current problems and after having devised a Future State you would like to achieve, you should move on to implementing it. Divide the improvement into manageable segments, so you your team can understand them better and devise your implementation plan in phases. Keep monitoring all key metrics while undergoing the transformation.
You can go to https://globalsixsigma.cn/six-sigma-training.php to learn more about our training solutions.