Change: How to Stop New Processes from Failing
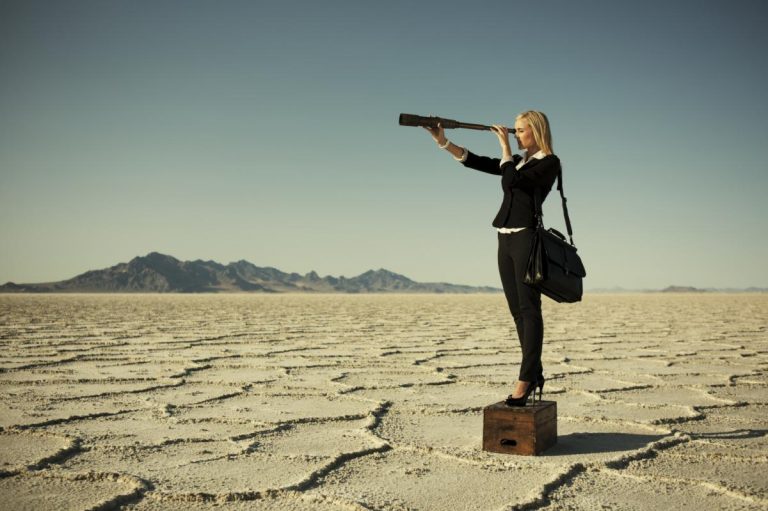
Imagine; it’s the end of the year, and your project team is about to unveil the numerous improvements made over the past four quarters. Excitement is in the air, executives are closely watching; this is the movement you have been waiting for. However, what happens next is not always what you expect or predict to occur. For most projects that implement changes into existing projects, failures will occur. However, the reason for system failure is not always simply a poorly designed process improvement. The leading cause of failures in new processes is people, specifically, the ones who must execute and manage the changes.
What Happens with Change?
Change is difficult for most people to comprehend. When employees have become set in their ways of operating a certain process, they will rarely embrace new innovations or improvements. Yet, we will always need changes. Whether to increase production efficiency, reduce waste, or to improve manufacturing speed, changes happen for any number of reasons. Although changes are necessary, it’s difficult to ensure their success. For Six Sigma professionals who carry out process improvement projects, there is a simple and effective method to integrate change easily and smoothly. In this article, we will discuss the CAP method, what it is, and how it can help prevent new processes from failing.
What is CAP?
As many know, General Electric (GE) was one of the founding companies for Six Sigma implementation. The company’s CEO in the 1990’s collaborated with Six Sigma champion Jack Welch to thoroughly integrate corporate-wide changes. Like many corporations and organizations, GE knew that change would be an up-hill battle. However, by fighting head on and instilling changes within the company’s culture, GE quickly adapted. Likewise, Welch fully supported the idea that disciplined change would lead to the greatest rewards from Six Sigma quality initiatives. By working with GE’s CEO, Welch developed the revolutionary plan known as the Change Acceleration Program (CAP).
In more detail, CAP helps organizations embrace and execute changes with the help of two strategies. The first of which is ‘Technical Strategy’. This strategy integrates the changes made by Six Sigma and the DMAIC method. Ultimately, change depends on the need it has. For Six Sigma projects, the DMAIC method focuses on producing a timeline that outlines what changes will be made and when. Additionally, project milestones and what resources the project needs are carefully outlined.
Next, there is ‘Cultural Strategy’. For every process change, people are involved. Because of this, project managers must focus on how they can communicate and encourage the changes to other team members. When everyone supports the project’s end goal, there is a greater chance of avoiding process failures. It’s important to address both the scientific needs of the project through the Technical Strategy. Whereas, you must also acknowledge the human element and facilitate all who are involved by using the Cultural Strategy.
When Do You Use CAP?
It’s best to use CAP for preparing an organization for upcoming changes, like how GE did. CAP helps any number of Six Sigma projects implement changes with the least resistance. Projects, such as those which impact multiple people or departments, require strategic approaches, or multiple functionalities greatly benefit from CAP. When you obtain the support of your employees, change is a manageable process. However, if employees resist the change, do not understand its benefits, or do not recognize their roles, change can become unattainable.