Xerox and Six Sigma: A Great Partnership
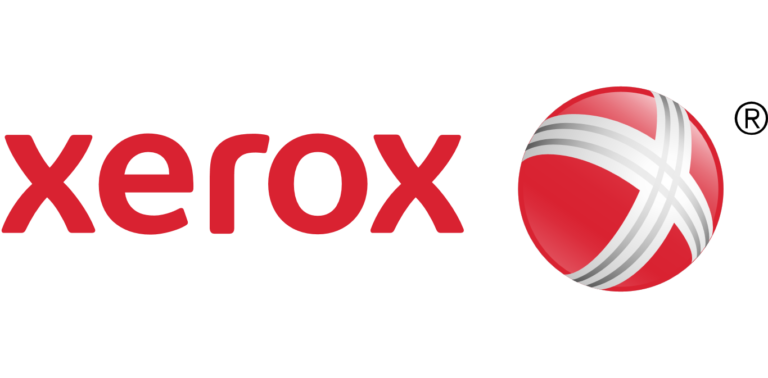
Xerox implemented Lean Six Sigma back in 2003, and needless to say (but we will say it anyway) with great success. The ripple effect that using Six Sigma as well as Lean strategies has had on all who do business with Xerox is startling.
We want to first bring up the fact that all of the successes we speak about on all the companies we have reported on are measurable improvements that are documented. In other words, all improvements are noted and tracked.
In a world of mass media and social media where things could get misinterpreted, Six Sigma and Lean is the real deal. In fact, the core of Six Sigma and Lean is based on fact, and all is data-driven.
Having said that, we do understand why some first-timers have apprehension, because there are so many “quick-fixes” based on the imagination of the person or company trying to sell their business improvement ideas. These ideas have tarnished the point of view of many business owners looking to make changes.
The Proof is Obvious
Xerox used Six Sigma on their internal processes to streamline; in other words, if it did not bring value to the company, they did away with it. This reduced variation and process errors, or defects. Then Xerox went ahead and applied Lean methods to eliminate waste and increase the process speed.
The ripple effect was felt by all of Xerox customers, from various industries such as finance, to government agencies and educational institutions.
Xerox made improvements by training thousands of their employees, leading thousands of projects and significantly contributing the total customer service aspect of the company. Over a period of time, the company showed massive, measurable improvements for Xerox, and the benefits reached all of their customers.
The 2018 schedule for 6sigma.us is now available! For more information on our Six Sigma training courses or services, please visit 6sigma.us.