The PDCA Cycle as Part of the Continuous Improvement Process
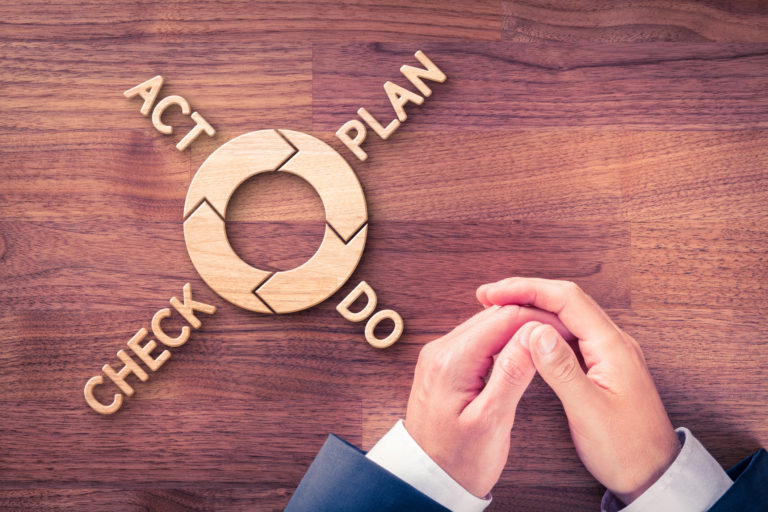
There are many great tools and templates used in Six Sigma, and today we are going to spend a little time with PDCA (Plan-Do-Check-Act). PDCA is a template or cycle used for problem solving. W. Edwards Deming originally created PDCA way back in the 1950s, and his intentions were to use PDCA with a continuous improvement procedure to help rebuild Japanese industries.
PDCA: The Problem Solving Cycle
P (Plan): In this stage, the purpose is to investigate the situation in its current stage. After you clarify the nature of the problem, define the problem that you want to fix. Identify potential root causes. Capture and analyze real data and write a mission statement.
D (Do): In this stage, you want to make the team aware of the gravity of the real problem. Use and analyze data currently found, and make sure you are defining and implementing a solution plan.
C (Check): Here you want to monitor and evaluate the effect of the current implementation. Seek countermeasures to improve the current solution. Once again, collect current data with the improvements in place and if need be, train those who are directly affected by the new solution plan.
A (Act): Continuously monitor the new performance measures, and decide if any adjustments need to be made. If adjustments need to be made, then integrate into the new working practice. If the solution is not working, then abandon the plan and ask the team what was learned from this and start a new PDCA cycle with a new target goal.
Problems usually accumulate over time, and if you use continuous improvement tactics (such as kaizen) as a normal part of the business culture, you will truly circumvent many serious issues.
Want to learn more about problem-solving techniques like PDCA? For more information on our Six Sigma training courses and services, please visit 6sigma.us.